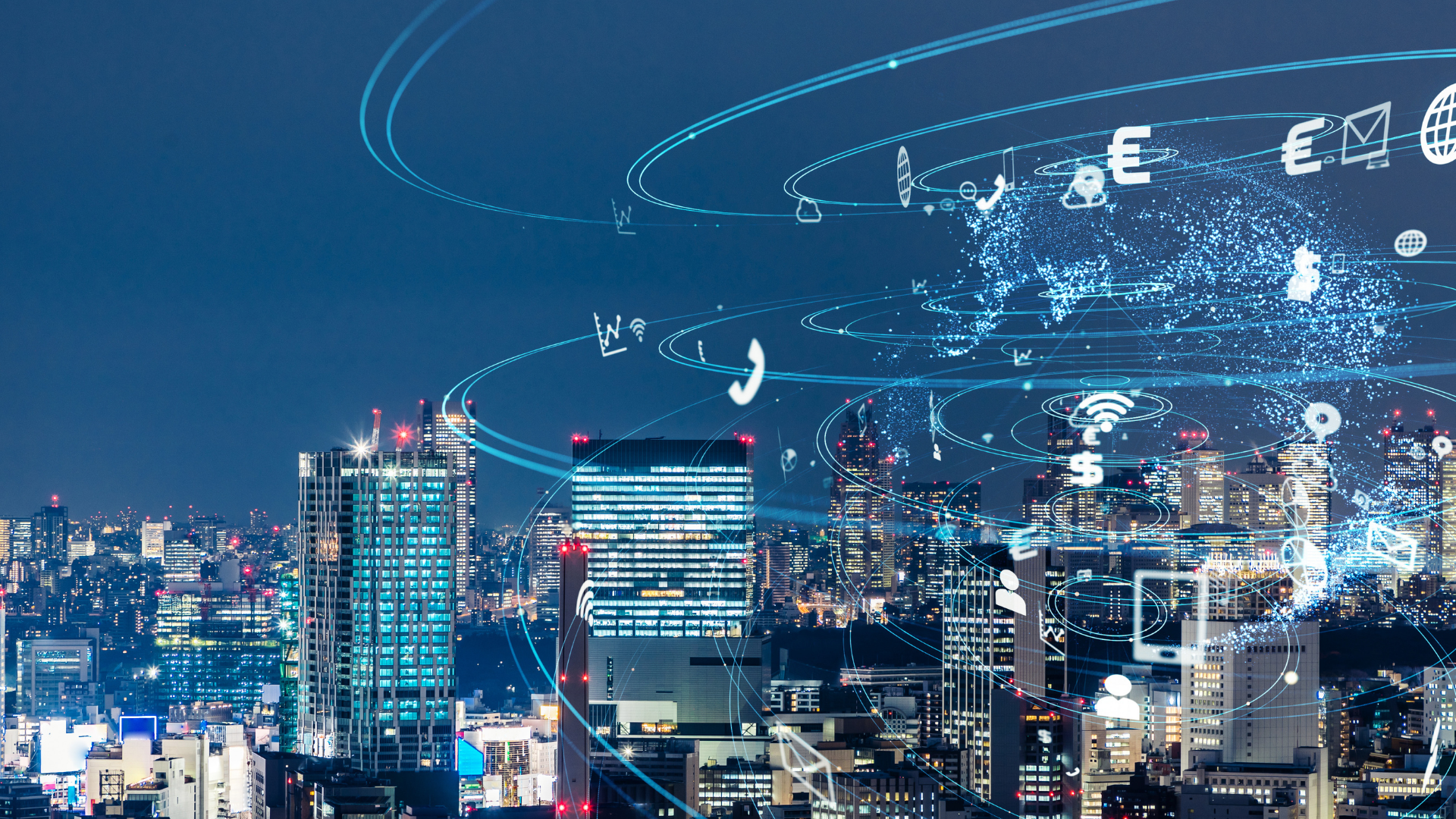
A indústria manufatureira foi fortemente afetada pela pandemia. No início, cerca de 1,4 milhão de pessoas perderam o emprego no setor, de acordo com o relatório da Deloitte e do Manufacturing Institute. Hoje, com o reaquecimento da economia e o retorno gradual das atividades presenciais, o cenário é outro: 2 milhões de vagas devem permanecer não preenchidas até 2030, custando até US$ 1 trilhão à economia norte-americana, por exemplo.
“Além das demissões por causa da pandemia, estamos experienciando uma leva de aposentadoria em massa”, contextualiza Joe Mulrooney, Manufacturing Industries Director na ServiceNow. Para tentar integrar a mão de obra necessária, as indústrias manufatureiras estão adaptando seus processos de contração e compartilhamento de conhecimento à nova realidade.
“A mão de obra emergente precisará lidar com dispositivos da Internet das Coisas Industrial (IIoT, na sigla em inglês), usar ferramentas analíticas para fundamentar suas decisões e supervisionar operações tecnologicamente avançadas – tudo isso enquanto mantém tudo funcionando e treina a próxima geração”.
Os executivos, portanto, devem se empenhar no desenvolvimento de uma força de trabalho conectada que utilize ferramentas digitais para simplificar processos e digitalizar conhecimentos, o que não significa afirmar que os trabalhadores serão substituídos pela tecnologia. Pelo contrário, “os trabalhadores fabris são uma parte essencial dessa jornada.
Afinal, melhores sistemas de planejamento de recursos empresariais (ERP), sistemas de execução de manufatura (MES), sistemas de gestão de manutenção computadorizada (CMMS), robôs, esteiras e maquinário ainda precisam de pessoas para funcionar”, explica Mulrooney. Confira a seguir quatro benefícios em empregar uma força de trabalho conectada no setor manufatureiro, de acordo com a ServiceNow:
- Redução de erros humanos – Nos próximos anos, as indústrias irão precisar integrar novos trabalhadores e requalificá-los por meio de treinamentos no próprio trabalho. Empregados experientes conseguem mudar rapidamente para uma linha de produção diferente ou colaborar com a equipe, mas os novos contratados precisam de uma ajuda extra. Enquanto estão se inteirando, esses novos funcionários têm o potencial de cometer erros.
De acordo com o Departamento de Energia dos EUA, de 80% a 90% das paralisações são causadas por erro humano. Para reduzir os erros humanos, as indústrias contam com procedimentos operacionais padronizados (SOPs) registrados em papel ou comunicados oralmente por funcionários.
Porém, com a atual escassez de mão de obra e com a rápida evolução das tecnologias industriais, as organizações não podem depender do papel e do conhecimento institucional. SOPs obsoletos podem até mesmo provocar condições perigosas de trabalho. Uma força de trabalho conectada que utilizar SOPs registrados digitalmente poderá achar com mais facilidade, coletar e transmitir informações.
Fluxos de trabalho digitais podem guiar perfeitamente os empregados na execução precisa de tarefas e procedimentos, sendo facilmente acessados a partir de um laptop ou dispositivo móvel. O registro e a transferência digitais de conhecimento previnem erros humanos, proporcionam treinamentos intuitivos para novos funcionários e permitem que os empregados acompanhem as mudanças nos processos.
- Eficiência turbinada – A criação de uma força de trabalho conectada quebra silos e contribui para uma melhor experiência de pessoal. Os funcionários necessitam se comunicar digitalmente e acessar informações em uma única plataforma – independentemente de estarem no escritório, no chão de fábrica ou fora da planta.
As indústrias devem considerar sistemas que permitam a conexão e a colaboração entre as áreas de ERP, MES, gestão de qualidade, atendimento ao cliente e gestão de relacionamento com o cliente (CRM). A colaboração facilitada e o contexto mais claro podem ajudar os empregados a tomar decisões melhores e mais rápidas, gerando eficiência em toda a equipe de produção.
- Melhoria na OEE e no COGM – Conectar operadores fabris com ferramentas móveis digitais faz com que o trabalho seja feito de forma mais rápida e melhor, a um custo mais baixo. SOPs digitais ajudam a garantir que mesmo os funcionários mais novos tenham o melhor desempenho possível. Os dados da IoT, antes restritos a painéis de gerenciamento, são transformados em fluxos de trabalho que orientam as ações no chão de fábrica.
Escalonamentos avisam os operadores para que deixem tarefas rotineiras não urgentes e se desloquem para onde são mais necessários. Pesquisas já mostraram que essas melhorias podem render um aumento significativo na eficiência geral de equipamentos (OEE) e uma redução no custo dos produtos manufaturados (COGM).
- Mais trabalho padronizado e conformidade de segurança – As indústrias estão sobrecarregadas pelo volume considerável de exigências regulatórias, desde o preenchimento de formulários até o envio de e-mails para que os documentos sejam assinados. Realizar tais tarefas on-line pode reduzir esse fardo. Quando tarefas rotineiras simples, como inspeções de 5S e de segurança, são digitalizadas, o sistema certifica-se de que nada esteja faltando.
Registros auditáveis, com marcação de data e horário, são armazenados na nuvem. Notificações e alertas são enviados para as equipes certas, com os devidos escalonamentos caso as respostas não ocorram no tempo certo. – Fonte e mais informações: (https://www.servicenow.com/).