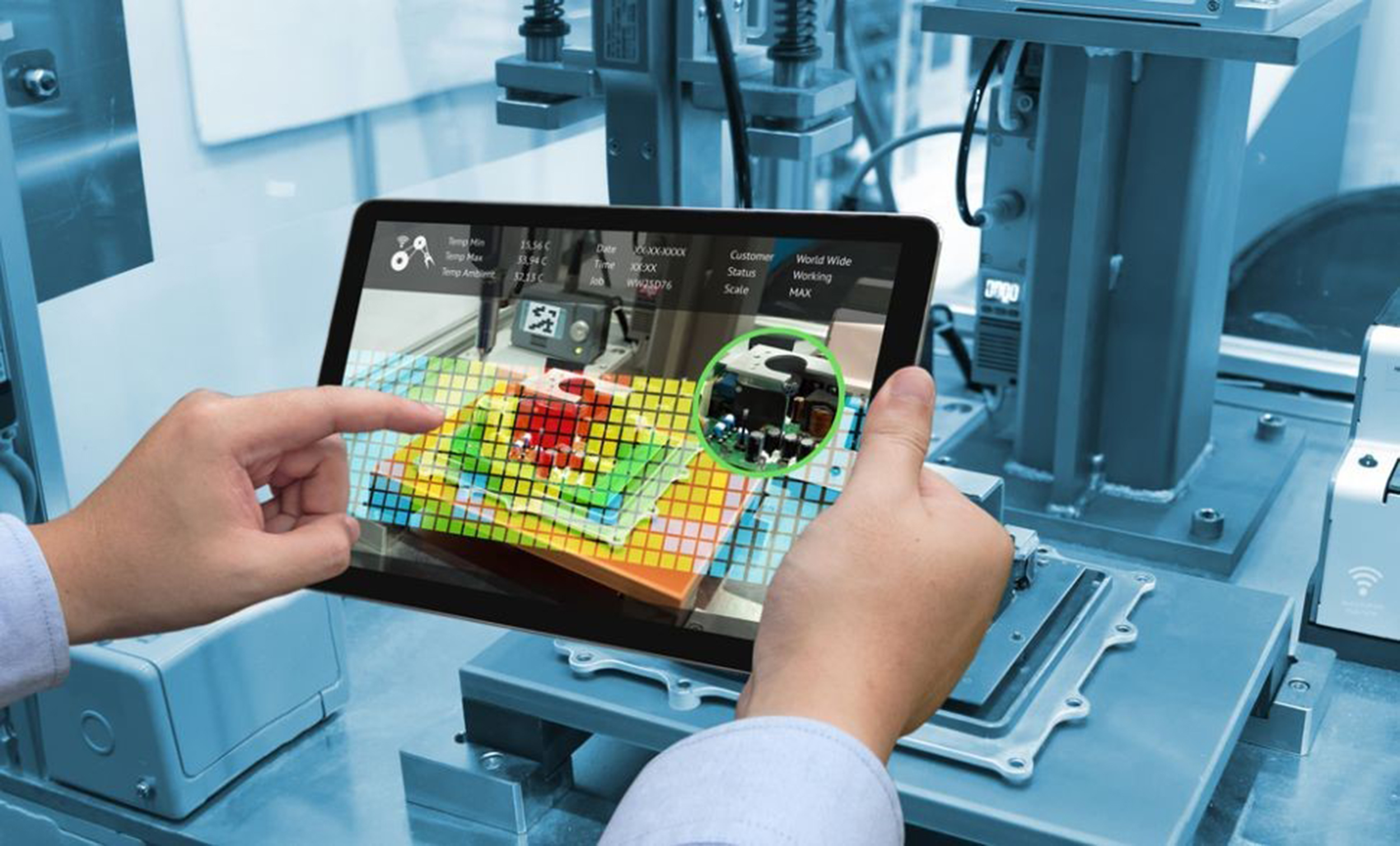
A Agência Brasileira de Desenvolvimento Industrial (ABDI) estima que a adoção de conceitos da Indústria 4.0 na matriz produtiva brasileira poderia gerar uma economia de R$ 73 bilhões ao ano no país, graças a fatores como ganhos de eficiência produtiva e redução do consumo de energia e de gastos com manutenção de maquinário.
É um panorama que até deve ser impulsionado pela atual crise. Só para se ter uma ideia, estudo da consultoria global de mercado de tecnologia ABI Research aponta a transformação digital como a principal aliada das empresas na difícil tarefa de equilibrar as contas internas no mundo pós-pandemia. A proposta engloba uma série de transformações digitais nos processos manufatureiros, por meio de recursos como inteligência artificial, big data, impressão 3D, internet das coisas e automações.
Mas, segundo Romeu Gadotti, gerente de Projetos da Supero Tecnologia – empresa de soluções em TI e alocação de mão de obra especializada – esse processo é bastante particular em cada organização e não há uma fórmula pronta, pois as dores e necessidades costumam variar.
“Em alguns casos, a solução é cara demais para o porte de investimento da empresa ou para o problema que ela tem, inviabilizando o retorno. Mas sempre há formas de balancear isso. O que vale para todas é que tecnologia por tecnologia não agrega valor. A solução precisa ter um objetivo, estar alinhada à estratégia de negócios”.
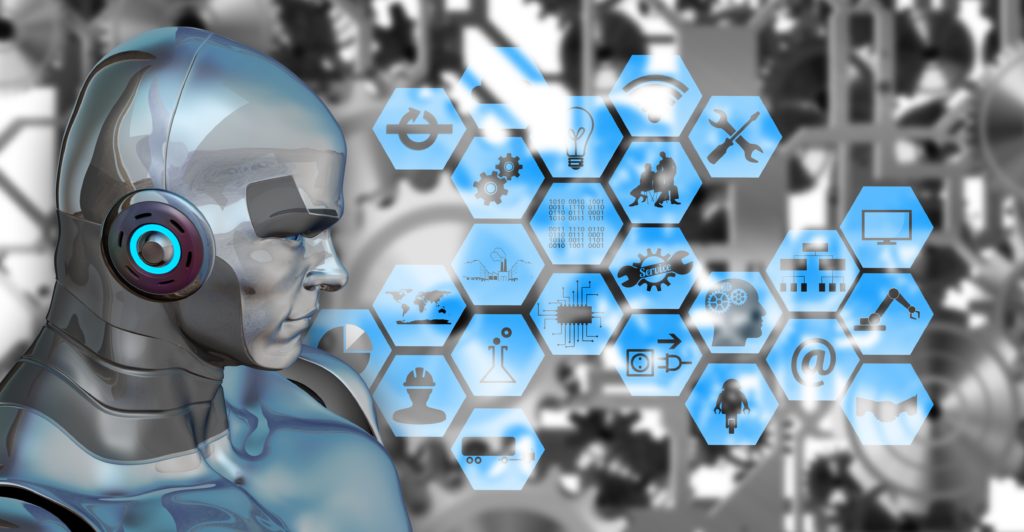
Essa transformação é uma jornada que deve ocorrer passo a passo, e eles não precisam ser grandes, explica o gerente de Projetos da Supero: “Clientes nos procuram buscando uma solução de Big Data e Business Intelligence para trabalhar os seus dados. Mas, antes de chegar nessa etapa, é preciso verificar se a coleta dessas informações reflete realmente o que está acontecendo na empresa, em suas linhas de produção”.
Guilherme Tortorella, especialista em integração entre Indústria 4.0 e Lean Management e professor do departamento de Engenharia de Produção e Sistemas da Universidade Federal de Santa Catarina (UFSC), observa que há um aspecto estrutural da economia brasileira que faz com que essa transformação ocorra em etapas: “Investimentos em longo são prazo são difíceis de serem feitos no Brasil, em razão da permanente instabilidade econômica”.
A seguir, um passo a passo para iniciar a integração à Indústria 4.0 com soluções simples e de baixo custo:
- Documentação – Empresas ainda têm muitos problemas pequenos, de dados que se perdem porque ficam num pedaço de papel ou planilha de Excel, que não foram consolidados e cruzados com outros dados, o que poderia gerar uma análise mais eficiente de alguma informação. “Eu só consigo gerar um novo conhecimento para uma tomada de decisão quando eu junto esses dados e dou a eles alguma lógica”, explica Gadotti.
É possível adotar sem grandes investimentos aplicações de computação em nuvem e também o uso de dispositivos móveis, que fazem parte do dia a dia dos trabalhadores e são de fácil manuseio, para otimizar a captura de dados e agregar valor à linha de produção.
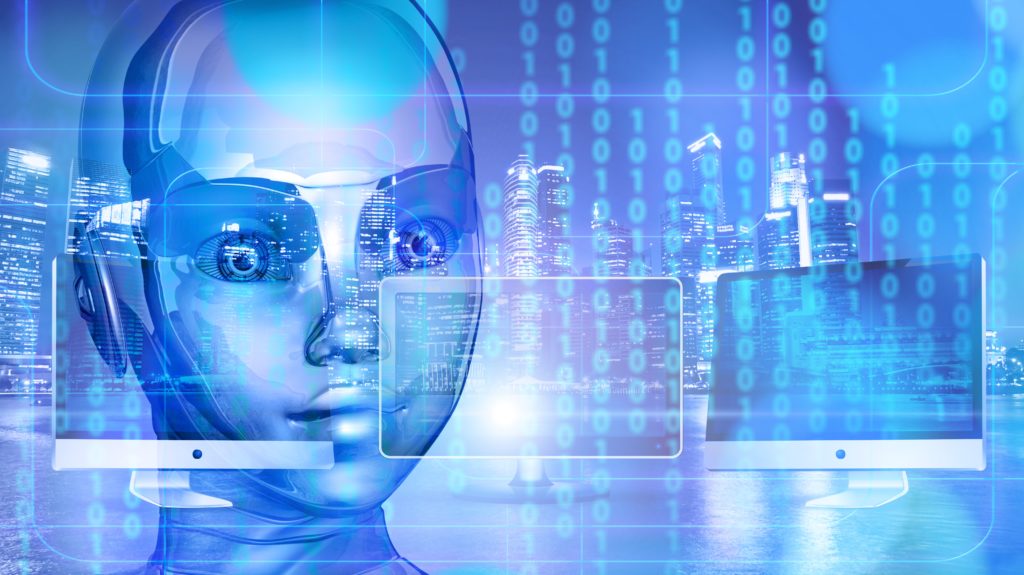
- Experiência do Usuário (UX) – Pesquisa da Confederação Nacional da Indústria (CNI) aponta que uma das barreiras à adoção de novas tecnologias é a falta de pessoas capacitadas para lidar com equipamentos e softwares. É possível contornar esse problema adotando a técnica de UX (User Experience) – que se refere a como, quando, onde e por que a pessoa utiliza determinada ferramenta e como ela se sente nesse processo. A técnica ajuda a melhorar a experiência do usuário e aumenta o engajamento.
- Rastreamento – Gestores de grandes empresas precisam monitorar a localização dos funcionários para evitar o acesso à áreas restritas. Isso pode ser feito com eficácia com sistemas de reconhecimento facial, que funcionam, inclusive, em pontos cegos onde não há sinal de telefonia móvel. Também há aplicativos de checkpoint de produto na planta, que podem funcionar via um sistema de leitura de código fixo ou com ajuda do funcionário da área, que registra por meio de uma foto o estado do produto ao chegar naquele seção, antes de ser despachado para outra.
- Custos – “Tudo em uma empresa deve ser calculado para que seja identificado quanto esforço é necessário para cada operação”, explica o gerente de Projetos da Supero. Para isso, há aplicativos para cálculo de custo de mão de obra. Eles ajudam a empresa saber, por exemplo, o tempo exato necessário para a realização de cada operação. Na prática, o cronômetro manual é substituído por um app que envia a informação por aplicativo móvel para uma base de dados, para processamento.
- Relacionamento com o cliente – Aplicativos podem criar canais sólidos de comunicação e relacionamento direto com o cliente, para que ele tire dúvidas durante o processo de produção do produto. No pós-venda, bots de resposta permitem uma validação do interesse e satisfação do cliente. “É importante a empresa saber se o que ela está produzindo está de acordo e se o cliente está satisfeito com a entrega”, complementa Gadotti.
Fonte e mais informações: (https://www.abdi.com.br/).