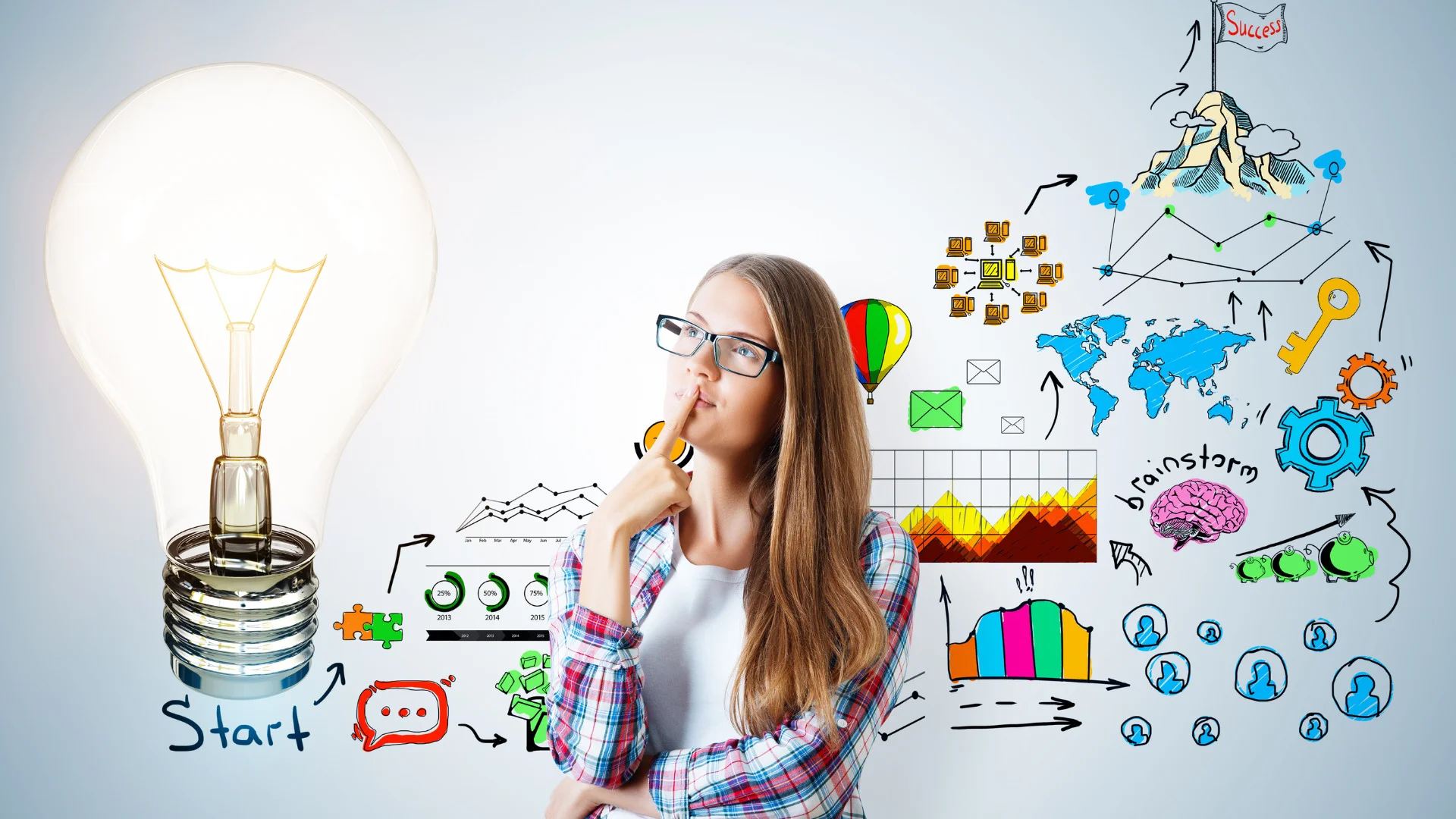
Douglas Campos (*) e Carlos Lobo (**)
Os desafios enfrentados pelas empresas são cada vez maiores na era da digitalização. No meio industrial, a transformação digital é também conhecida como a Indústria 4.0, termo que surgiu na Alemanha, em 2011. Nessa jornada, empresas devem focar não somente em inovações radicais, mas também nas incrementais, que sustentam o negócio em curto prazo.
A inovação de processos pode ser usada para aumentar a competitividade em um mercado sempre mais dinâmico. Nessa corrida pela melhoria contínua, muitos gargalos nas operações não são observados, ou mesmo, quando vistos, são deixados de lado, devido à falta de foco e de outras prioridades dos times no dia a dia.
Os projetos de inovação de processos precisam ser implementados após avaliações criteriosas tanto do segmento de atuação da organização quanto do processo interno de produção. São decisões estratégicas, que partem do topo da organização. No entanto, nessa jornada, assim como existem fatores motivacionais para implementar estratégias, também existem barreiras. Alguns desafios envolvem, por exemplo, a falta de conhecimento, de recursos financeiros ou humanos, entre outros.
O fato é que, não adotar novas tecnologias ou metodologias para aumentar a produtividade pode se mostrar bastante custoso. A ABDI (Agência Brasileira de Desenvolvimento Industrial) calcula que a implementação de soluções da chamada Indústria 4.0 poderia trazer redução de custos de mais de R$ 70 bilhões por ano.
Para pegar carona no avanço constante da tecnologia, primeiramente é preciso realizar um value stream mapping (VSM). Hoje, consultorias fazem mapeamento completo do fluxo de valor, o que possibilita a construção de uma visão comum do sistema de produção da empresa. Essa é uma chave para analisar as dores da companhia de forma assertiva.
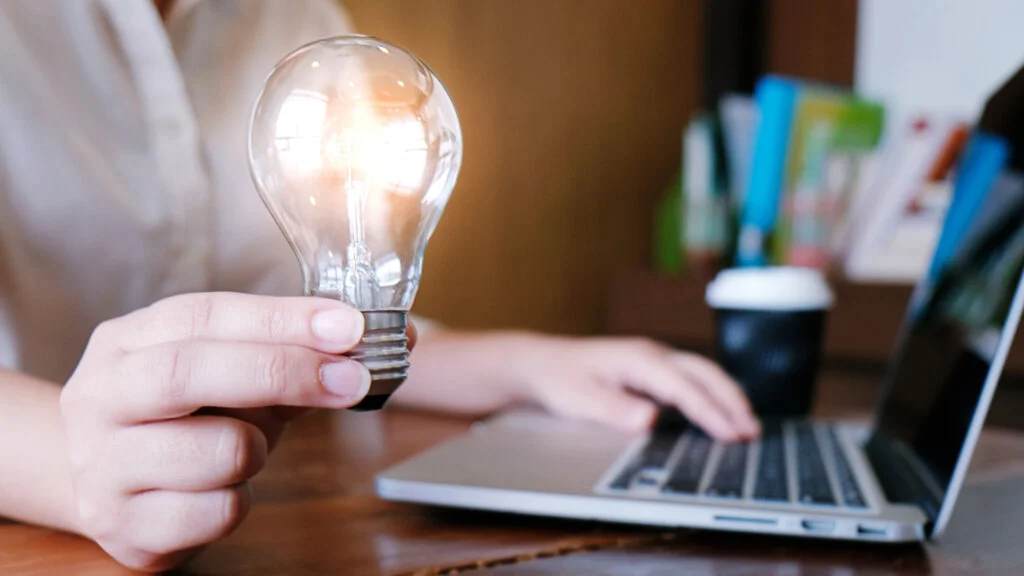
Além disso, o mais importante nesse modelo é não focar no problema em si e concentrar a discussão em sua causa-raiz para definir a melhor maneira de eliminar o contratempo. Vale reforçar que esse mapa de processo não representa apenas o fluxo de material em produção, mas também o fluxo de informações – desde o cliente, passando pela operação e terminando no fornecedor. Cabe reforçar que o VSM é um modo diferente de observar o sistema produtivo.
Os indivíduos estão acostumados a notar os problemas, mas não a enxergá-los como adversidades. Isso porque é comum não avistar o que não se está procurando. Esse é o caso da maior parte do segmento industrial no Brasil. Tipicamente, a mão de obra direta utilizada nas fábricas do país conta com grande potencial de melhorias. Assim como em outros lugares do mundo, o esforço para ganhar produtividade é maior quando se considera a tecnologia empregada.
Entretanto, quando se avaliam as atividades típicas de um operador de fábrica, constata-se o quanto é possível economizar com a eliminação de erros comuns na rotina desses profissionais. Aqui a melhoria contínua pode contribuir para reduzir esses desperdícios. A cultura desse conceito deve ser a base das empresas para alcançarem mudanças por meio de inovações mais radicais.
Estudos indicam que, na atuação automática do dia a dia, pode-se chegar a ter mais da metade do tempo de trabalho dedicado a atividades que não deveriam existir. Ações rotineiras que só acontecem devido aos problemas não resolvidos, ou às ineficiências. Claro que eliminar essas atividades requer entender as causas e trabalhar nelas.
Muitos pesquisadores já afirmaram que “JIT is about flow”. Ou seja, a grande inovação que os japoneses fizeram na Toyota, por exemplo, e que se popularizou no mundo como lean manufacturing, foi o fluxo contínuo operacionalizado pela célula de produção. Um case interessante foi o projeto conduzido na Autocam, multinacional fabricante de componentes automotivos usinados de alta precisão, para aplicações nos sistemas de direção, transmissão, injeção, freios, motores elétricos, turbos, entre outros.
Trata-se de componentes críticos para as áreas citadas. Atualmente, a Autocam faz parte do grupo NN Inc., presente em quatro continentes, com mais de 4 mil funcionários em 26 fábricas e mais de 2 bilhões de componentes produzidos anualmente. Além disso, a NN Inc. atua em diversos segmentos além do automotivo, como no aeroespacial e defesa e na área médica. No Brasil, a Autocam possui três fábricas no estado de São Paulo.
Nesse caso, o desafio era relacionado ao aumento de capacidade assim como à necessidade de aumento de produtividade. Eram grandes obstáculos operacionais em uma área de produção relevante, em que o cliente final era uma montadora. Após a consultoria e a efetiva aplicação da metodologia com o time da empresa, 25% da mão de obra direta foi reduzida; a distância percorrida pelos componentes durante a produção foi cortada em 50% e a área total utilizada diminuiu 30%.

Além de atingir as metas de capacidade, também foi possível obter a melhoria dos indicadores de qualidade com a padronização dos métodos de trabalho e o ajuste das máquinas operatrizes. Segundo depoimentos do time gerencial da empresa, a cultura da melhoria contínua e da inovação foi absorvida não somente pela equipe que trabalhou no projeto, mas também pelas demais áreas de suporte.
De acordo com os dados da consultora norte-americana ABI Research, até 4 milhões de robôs e máquinas operarão em mais de 50 mil armazéns em todo o mundo em 2025, já em 2018 o número aplicado à robótica era de apenas 4 mil. Nesse sentido, a automação é um caminho sem volta, independentemente do segmento de atuação, mas pode ser aplicada de maneira muito mais profissional quando aliada a outros processos.
O ser humano não será completamente substituído, mas, sim, cada vez mais auxiliado pela automação. Todas as tarefas simples e repetitivas tendem a ser automatizadas, enquanto o ser humano será utilizado em atividades sensíveis que exijam habilidade e discernimento. As empresas precisam traçar metas operacionais concretas, ligadas aos resultados financeiros, criar equipe de projeto e contar com um especialista externo para trazer visões distintas e questionamentos novos.
Em uma sociedade 5.0, é preciso pensar na jornada completa e apresentar soluções que atendam às necessidades viscerais do negócio, sempre com um olhar atento e inovador.
(*) – É COO da Mobile Solution, da NN Inc (www.nninc.com). (**) – É especialista em lean e sócio da Hand (www.handgc.com.br).