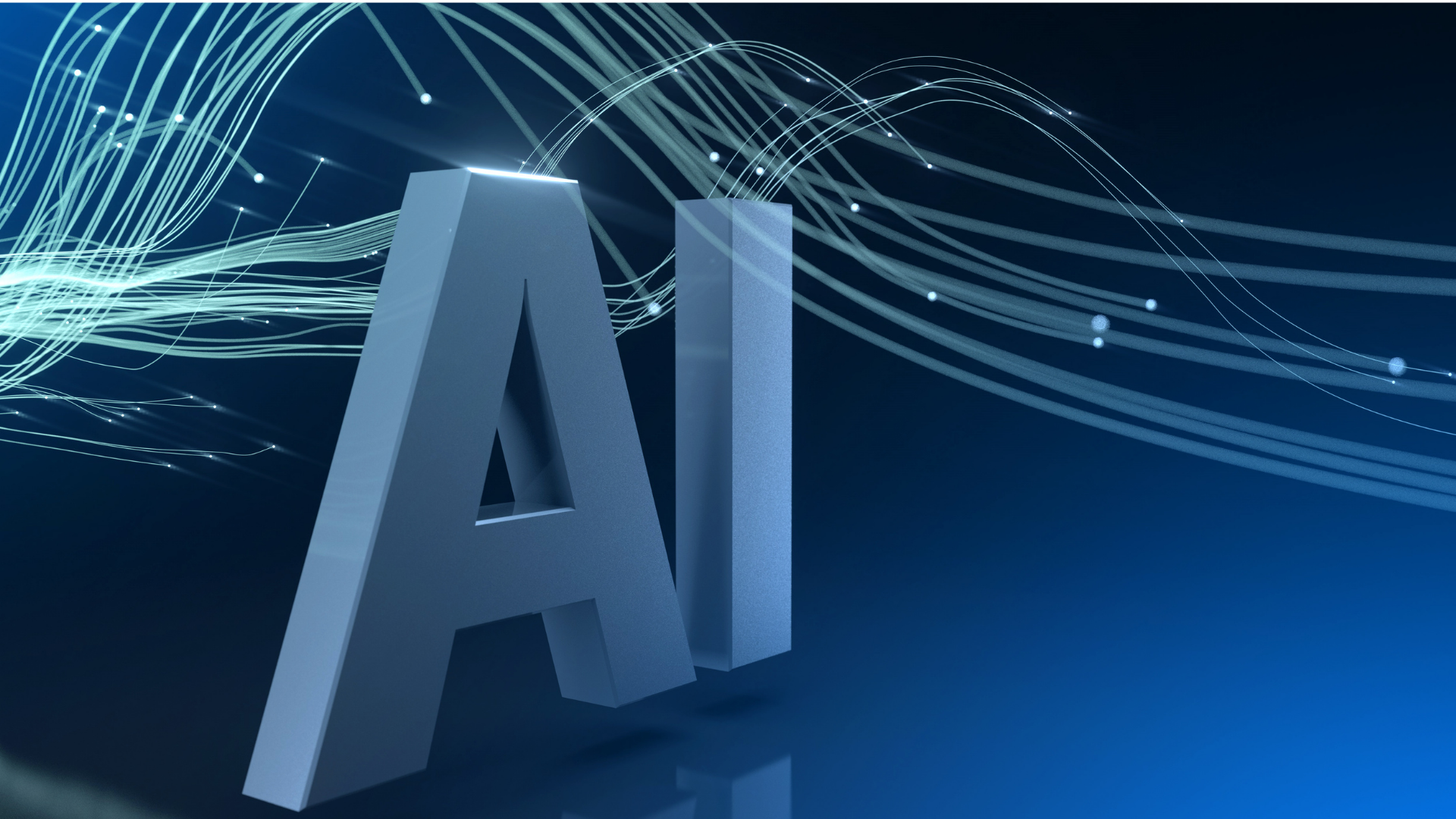
Matthias Roese (*)
A introdução da inteligência artificial (IA) na produção geralmente falha durante a transição da prova de conceito (PoC) para a operação regular. Isso só pode ser evitado com uma abordagem holística que leve em consideração todo o espectro de dependências comerciais, técnicas e organizacionais.
Vamos considerar uma empresa metalúrgica cujos processos são altamente automatizados. Um sistema de armazenagem fornece a chapa metálica solicitada, os sistemas de transporte a entregam diretamente às máquinas de corte, puncionadeiras, prensas e sistemas de soldagem, e uma verificação de qualidade ocorre após cada etapa de processamento. No entanto essa automação baseada em regras está se tornando cada vez mais um problema.
Nos últimos anos, os tamanhos dos lotes de nossa empresa metalúrgica tornaram-se cada vez menores – devido à mudança na demanda dos clientes e, mais recentemente, devido a gargalos de entrega. Cada nova peça a ser fabricada requer um novo amaciamento da linha de produção – e os parâmetros devem ser determinados e testados para cada etapa individual do processo. Esse esforço anula os ganhos de produtividade da automação e a eficácia geral do equipamento (OEE) diminui.
Os idealizadores do conceito da Indústria 4.0 tinham cenários como esse em mente quando definiram o princípio orientador dos sistemas de fabricação autônomos e auto-organizados – que idealmente permitem que as cadeias de valor tenham a eficácia da produção em massa mesmo com tamanho de lote 1.
Com isso, a IA foi de fato declarada o motor da quarta revolução industrial. A IA dá exatamente o passo da automação baseada em regras para o autocontrole situacional e somente a IA é capaz de tirar conclusões de forma autônoma de dados históricos e em tempo real para reagir de forma adequada, precisa e rápida a eventos não planejados.
Contudo, após vários anos e relatórios de analistas, o cenário pode parecer um pouco frustrante. Embora a adoção geral da IA continue aumentando – de acordo com o McKinseys “State of AI in 2021” –, a fabricação ainda está muito atrasada. Uma das principais razões para isso é que um grande número de projetos de IA não vai além de uma fase de teste, a chamada prova de conceito (PoC).
As causas desse fracasso são mais profundas do que, por exemplo, falta de conhecimento ou orçamento – em muitos casos, as empresas de manufatura subestimam os desafios sistemáticos da introdução da IA. A maneira como as PoCs são configuradas é apenas um sintoma disso. Elas geralmente ocorrem em um ambiente protegido e estão focadas na aplicação e no treinamento dos modelos de IA com dados – mas a necessidade de integrar a solução de IA à tecnologia de informação e à produção existente e seus processos é muitas vezes negligenciada.
Isso inclui, por exemplo, o gerenciamento do ciclo de vida de aplicativos e dados, segurança, planejamento operacional e processos de controle e segurança operacional. Como resultado, a PoC não fornece evidências sérias de viabilidade técnica nem pode ser usada para calcular um business case sólido.
Por mais chato e tedioso que possa parecer, a introdução da IA na fabricação só pode ser bem-sucedida com uma abordagem holística. A PoC deve ser a ponta do iceberg – o resultado de uma série de decisões e projetos subjacentes, em que as iniciativas são derivadas de estratégias que são implementadas por meio de atividades de transformação técnica, organizacional e cultural.
Uma abordagem holística para a introdução da IA na fabricação inclui aspectos como o valor agregado que, ao ser usada a IA, é criado por meio de informações e insights, e ações e processos (autônomos) deles derivados. Os dados disponíveis são a base para isso – entretanto os dados não necessariamente se tornam informações úteis apenas pela aplicação da IA.
Eles só se tornam informações úteis se forem processados em um contexto específico e para um propósito específico. A análise de criação de valor avalia os benefícios das informações obtidas com a ajuda da IA, determina a qualidade dos dados e o esforço de aquisição e processamento deles, bem como os investimentos associados à produção operacional – incluindo custos de processo, tecnologia e pessoal. O resultado é o modelo de negócios ou caso de negócios.
Se a análise de valor chegar a um resultado positivo, inicia-se o desenvolvimento e a introdução do aplicativo de IA. Isso deve seguir uma filosofia de DevOps na qual todas as equipes relevantes de produção e operações, e também especialistas em IA e TI, trabalham juntos (no contexto de IA, isso também é chamado de MLOps e DataOps) – o que garante que a integração dos processos de TI e fabricação seja levada em consideração desde o início. O design da solução primeiro define o método de IA e o software a ser usado, assim como os dados de treinamento e sua preparação.
Os processos ocorrem em ambientes de TI e manufatura que são altamente fragmentados em muitas empresas – ou seja, não há acesso contínuo a ferramentas e dados, processos não coincidem, padrões e conceitos de segurança integrados estão ausentes. Esse ambiente é mortal para qualquer implementação de IA.
A base para resolver esse problema é a introdução de uma arquitetura centrada em dados. Em sua essência, ela dissocia os dados dos aplicativos que os geram, canalizando-os por meio de um hub de dados central. Cada aplicativo atua como um “produtor” de dados para o hub de dados, cada consulta é um “consumidor” do extenso banco de dados distribuído. Tudo isso está incorporado em uma estrutura abrangente de governança de dados.
Em muitos casos, as AI PoCs são configuradas de forma unidimensional porque são realizadas por cientistas de dados que entendem muito sobre dados e modelos, mas menos sobre arquitetura de sistema e processos de TI – e quase nada sobre os processos em uma fábrica.
Uma introdução bem-sucedida de IA requer a combinação certa de habilidades de diferentes departamentos para planejar, desenvolver, implantar e colocar em operação o próprio aplicativo e sua integração aos processos de TI e produção, contando com analistas de negócios, cientistas de dados especialistas em aprendizado de máquina engenheiros de dados engenheiros de software e um gerente de projeto. A boa notícia é que há uma transição contínua da automação para a autonomia. Isso pode ser demonstrado pelo exemplo da empresa metalúrgica mencionada.
Ela começou a complementar sua automação baseada em regras com métodos de IA e, gradualmente, converteu o acoplamento serial das estações de processamento em um sistema de estações de trabalho controláveis de forma flexível converteu o acoplamento em serie das estações de processamento em um sistema de estações de trabalho controláveis de forma flexível.
O próximo passo é permitir que o sistema atue de forma autônoma. Por exemplo, os resultados da inspeção de qualidade devem, se necessário, desencadear um ajuste dinâmico, independente e transversal dos parâmetros. Especialmente quando se trata de soldagem, faz sentido aplicar o aprendizado de máquina nas etapas anteriores do processo ou até mesmo em todo o processo de fabricação.
Para otimizar o aproveitamento da matéria-prima, a empresa planeja implementar uma conexão inteligente com o sistema de gestão de armazém e entrada de pedidos. Para a maioria das empresas, ainda há um longo caminho a percorrer para que essa metalmecânica alcance a visão de produção totalmente autônoma – porém, por meio da abordagem holística descrita, garante que realmente se avance nesse caminho.
(*) – É Diretor Global da Hewlett Packard Enterprise (www.hpe.com).